 |
|
Screen Mask: the patterning tool for screen printing
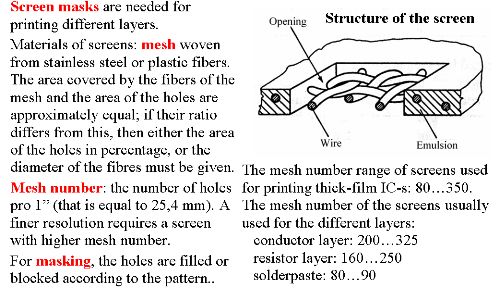
In thick film technology the various layers are usually deposited by screen printing onto ceramic substrates, using special pastes or inks, and screen masks (stencil screens) to define the layer pattern.
The screen is a woven mesh material made of stainless steel or plastic fiber. The screen mask is the screen with polymer (gelatin, called emulsion) or metal coating that fills unnecessary openings of the screen, thus results in a mask with well-defined windows (openings). The screen mask is stretched out by the screen frame that is made from metal, generally from aluminum. The frame with the screen mask is positioned parallel to the substrate, with a usual distance of 0.6 - 1 mm in between. In case of applying a metal (stencil) mask, it is positioned to be in contact with the substrate surface.
Screen texture
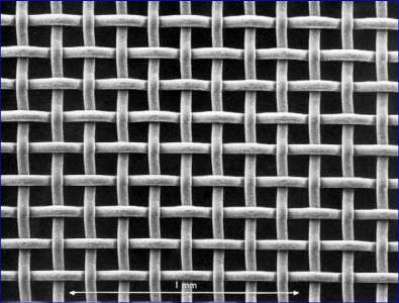
Screen mask: a screen with patterned emulsion layer
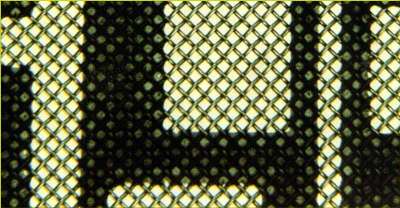
The screen material is characterized by the thread diameter and the mesh count. The term "mesh" refers to the openings and fractional parts of an opening, per inch, counting from the center of any wire to a point exactly 1 inch away. The mesh count therefore is the number of open spaces (or threads) per lineal inch. Generally, 80 - 400 mesh screens are applied in thick film technology. Masks made of screens with larger mesh count are thinner and suitable for finer pattern resolution, while low mesh count screen masks can be used for thick layers with rough patterns.
Conductor layers are printed using 200 - 325 mesh screens, resistors are prepared by 160 - 250 mesh screens and 80 mesh screens are used for solder pastes.
|