Thick Film Firing Temperature Profile
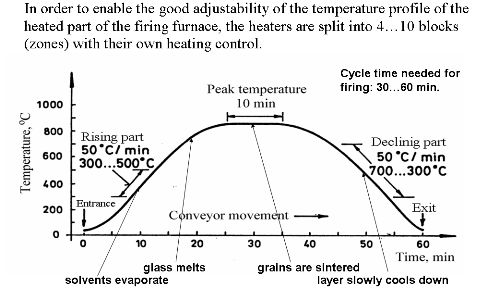
After drying, the firing process needs three phases, as follows: preheat and burnout; fire; cool and anneal. The 4 - 10 independently controlled heated zones of the furnace provide the suitable position-temperature and - as a consequence - the time-temperature profile for these three phases.
The organic binders and solvents burn out in the first preheating phase of firing, where the temperature rise is in the range of 50 deg C/min.
On firing, the individual grains of the dispersed glass melt, thus forming a matrix structure in which the metal grains are lodged to form conductive chains.
In addition, the molten glass wets the surface of the substrate and flows into any small surface irregularities, so that on cooling, good adhesion between the metal layer and the ceramic is ensured. The metal oxides of the glass also react chemically with the substrate material that causes further improvement of adhesion.
During this second phase when the glass frits melt, they compress and sinter the powder particles of the active material to one another, anchor the film to the substrate, and protect the active constituents from the environmental effects. In this phase, in addition to sintering, physicochemical processes - such as oxidization or reduction and recrystallization - are taking place to develop the required characteristics of the fired layer. Cermet - ceramic-metal composite - thick film pastes usually require firing at 600 - 1000 deg C, a typical 850 deg C peak temperature for 5 - 15 minutes, with an extremely accurate value within +-1 - +-2 deg C. For polymer-metal (e.g. epoxy-silver) composite layers, called polymer thick films, a much lower peak temperature of 150 - 250 deg C is required.
Controlled cooling to the room temperature is the third phase of the drying and firing process, with a declining temperature of -50 deg C/min, to avoid generation of cracks in the layer, and to provide time for annealing and stabilization.